Comprehensive Guide: What is Porosity in Welding and Exactly How to stop It
Comprehensive Guide: What is Porosity in Welding and Exactly How to stop It
Blog Article
The Science Behind Porosity: A Comprehensive Overview for Welders and Fabricators
Recognizing the detailed mechanisms behind porosity in welding is critical for welders and makers pursuing impeccable craftsmanship. As metalworkers look into the depths of this phenomenon, they uncover a globe governed by numerous elements that influence the formation of these minuscule gaps within welds. From the make-up of the base materials to the intricacies of the welding process itself, a wide variety of variables conspire to either exacerbate or reduce the presence of porosity. In this thorough overview, we will certainly unravel the scientific research behind porosity, exploring its effects on weld high quality and unveiling progressed techniques for its control. Join us on this journey through the microcosm of welding blemishes, where accuracy meets understanding in the pursuit of remarkable welds.
Understanding Porosity in Welding
FIRST SENTENCE:
Examination of porosity in welding reveals important understandings right into the honesty and top quality of the weld joint. Porosity, characterized by the existence of dental caries or gaps within the weld steel, is a common concern in welding processes. These voids, if not correctly attended to, can jeopardize the architectural honesty and mechanical residential properties of the weld, bring about prospective failures in the ended up product.

To detect and quantify porosity, non-destructive testing approaches such as ultrasonic testing or X-ray evaluation are commonly utilized. These techniques enable the recognition of inner flaws without jeopardizing the integrity of the weld. By assessing the size, form, and circulation of porosity within a weld, welders can make enlightened choices to improve their welding processes and accomplish sounder weld joints.
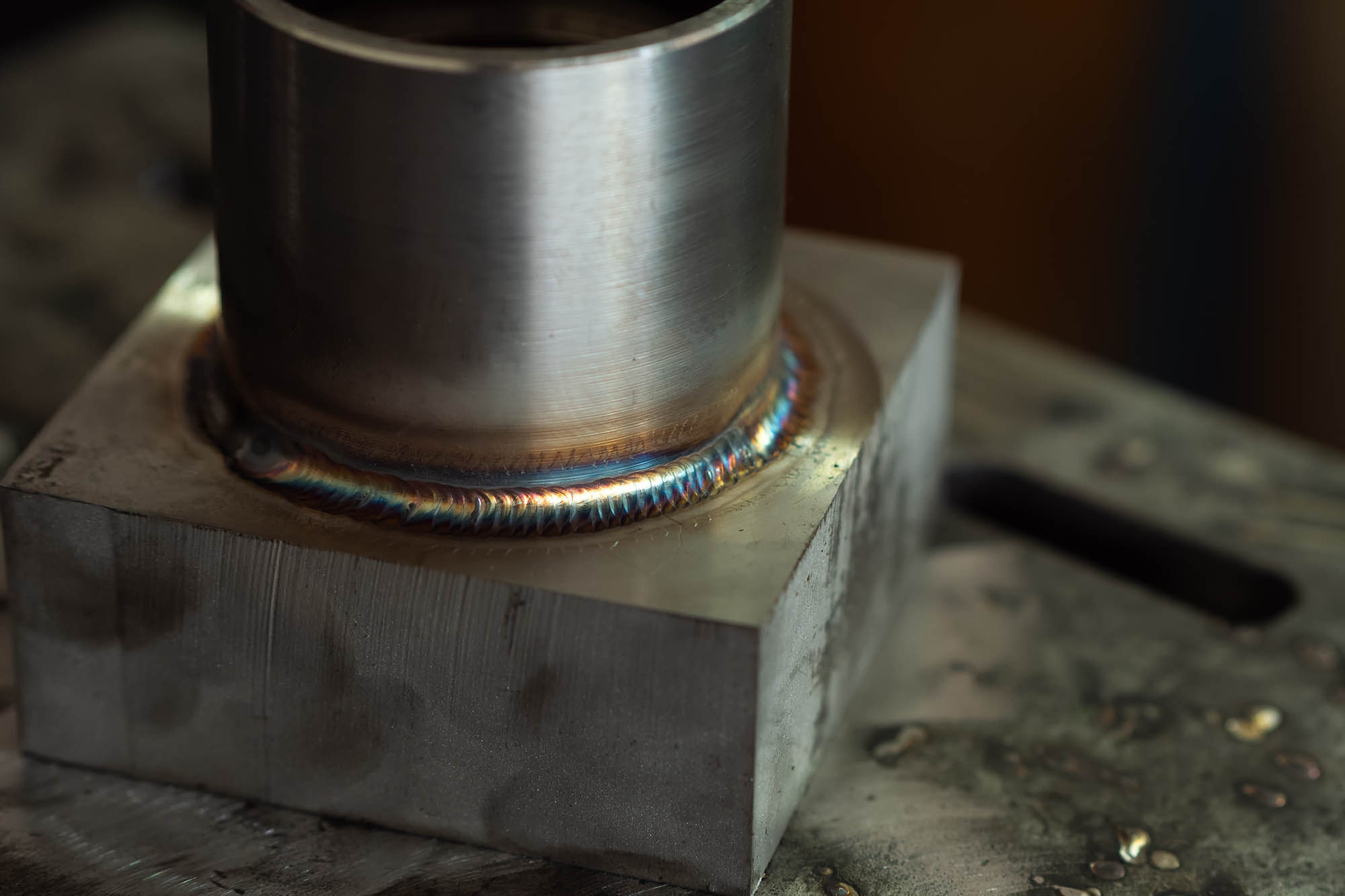
Factors Affecting Porosity Formation
The event of porosity in welding is influenced by a myriad of factors, varying from gas shielding performance to the intricacies of welding criterion settings. Welding criteria, consisting of voltage, current, take a trip rate, and electrode kind, additionally effect porosity development. The welding method used, such as gas steel arc welding (GMAW) or secured steel arc welding (SMAW), can influence porosity formation due to variants in warmth circulation and gas protection - What is Porosity.
Results of Porosity on Weld Top Quality
The presence of porosity likewise deteriorates the weld's resistance to corrosion, as the caught air or gases within the voids can react with the surrounding atmosphere, leading to degradation over time. Furthermore, porosity can prevent the weld's ability to hold up against stress or influence, more jeopardizing the overall quality and reliability of the bonded structure. In important applications such as aerospace, automotive, or structural constructions, where safety and resilience are vital, the destructive impacts of porosity on weld top quality can have serious repercussions, highlighting the importance of lessening porosity through proper welding strategies and procedures.
Strategies to Decrease Porosity
Furthermore, utilizing the suitable welding parameters, such as the correct voltage, present, and travel speed, is vital in preventing porosity. Maintaining a regular arc size and angle throughout welding additionally assists lower the likelihood of porosity.

Moreover, picking the ideal shielding gas and preserving appropriate gas circulation prices are crucial in lessening porosity. Making use of the ideal welding method, such as back-stepping or using a weaving movement, can also help disperse warm equally and decrease the possibilities of porosity formation. Guaranteeing correct air flow in the welding atmosphere to get rid of any type of possible resources of contamination is important for attaining porosity-free welds. By carrying out these strategies, welders can effectively decrease porosity and produce top notch welded joints.
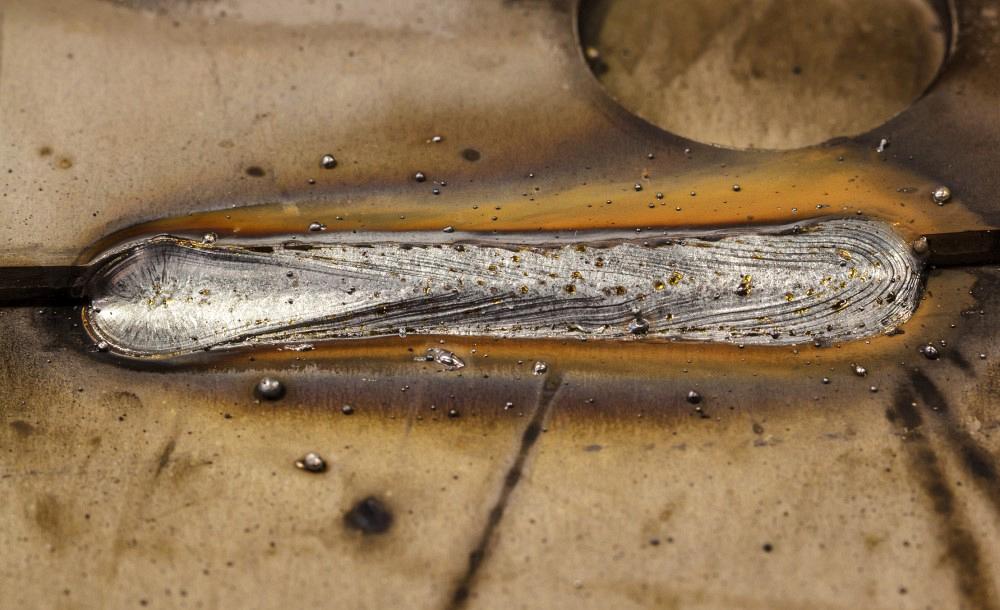
Advanced Solutions for Porosity Control
Applying advanced innovations and ingenious techniques plays a crucial role in achieving superior control over porosity in welding processes. Furthermore, using advanced see welding strategies such as pulsed MIG welding or customized environment welding can additionally assist alleviate porosity issues.
Another sophisticated option entails the usage of advanced welding equipment. For example, making use of tools with integrated attributes like waveform control and innovative source of power can improve weld top quality and reduce porosity risks. The execution of automated welding systems with exact control over specifications can substantially lessen porosity problems.
Additionally, incorporating innovative tracking and inspection innovations such as real-time X-ray imaging or automated ultrasonic screening can help in identifying porosity early in the welding procedure, allowing for instant rehabilitative actions. In general, integrating these innovative options can considerably enhance porosity control and enhance the total high quality of welded parts.
Final Thought
To conclude, recognizing the scientific research behind porosity in welding is necessary for welders and producers to produce high-grade welds. By determining the factors affecting porosity development and carrying out techniques to lessen it, welders can Homepage improve the total weld quality. Advanced remedies for porosity control can even more check it out boost the welding process and make certain a strong and reliable weld. It is crucial for welders to continuously inform themselves on porosity and implement finest techniques to achieve ideal outcomes.
Report this page